Sorry, this entry is only available in Tiếng Việt.
(Tiếng Việt) PHÂN TÍCH LOB (LINE OF BALANCE) – PHÂN TÍCH TIME STUDY
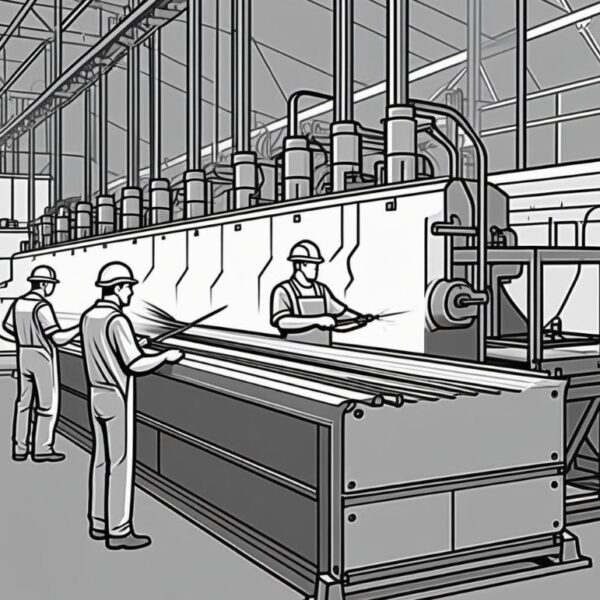
The American Society of Mechanical Engineers (ASME) provides standards for dimensioning and tolerancing across various engineering applications, including the development of gages and fixtures. These principles, outlined in ASME Y14.43, provide guidelines to ensure that gages and fixtures are manufactured to a high level of precision, helping to ensure that the components they measure meet the required tolerances.
Below are the main principles of dimensioning and tolerancing for gages and fixtures according to ASME standards:
Gages and fixtures are designed for repeated use, meaning they must meet strict tolerance levels to ensure consistent measurement accuracy. Design specifications must consider interchangeability, ensuring that each gage can measure parts within the required tolerance limits, even with slight variations in production.
ASME standards, particularly Y14.5, guide the application of GD&T principles on gages and fixtures. This includes specifying tolerances for form, orientation, location, and runout, which are critical for precise alignment and measurement.
Material condition modifiers are essential in defining the tolerance ranges for different material conditions. MMC (Maximum Material Condition) and LMC (Least Material Condition) are applied to set tolerance limits, especially for functional gages that check parts under assembly conditions.
Example: A hole in a component may need to be inspected at MMC (Maximum Material Condition) to ensure it is not too small. The gage used to inspect this hole will be sized at the maximum allowable dimension, ensuring that if the hole is large enough for the gage to pass through, it meets the required tolerances.
Functional gages are designed to simulate the mating conditions of parts in an assembly. They ensure that if a part fits the gage, it will also fit its mating part. This principle ensures that critical features, such as holes and shafts, meet the required tolerances.
Datum reference frames are essential reference points in GD&T and are necessary for consistently locating parts in fixtures and gages. The accurate selection and alignment of datums help maintain measurement consistency and accuracy.
Example: When designing a fixture for a flat surface on a metal block, reference planes (datums) will be established from specific edges of the block to accurately position it within the fixture. These datum points help consistently align the metal block throughout the measurement and inspection process.
When designing fixtures, it is necessary to consider tolerance stack-up, which refers to how individual tolerances accumulate during assembly. Accumulated tolerances are evaluated to ensure that the final dimensions remain within acceptable limits.
Gages must also comply with the necessary tolerances for inspection. This includes establishing a verification process for the gages to ensure they remain accurate over time due to high usage frequency.
Regular calibration and maintenance of gages and fixtures are essential to ensure they meet ASME standards over time, minimizing measurement errors and maintaining the reliability of the measurement system.
TASVINA is a company specializing in providing comprehensive solutions for design and machining, as well as the measurement and inspection of Gauges & Fixtures.
Contact: Nguyễn Xuân Cảnh (Mr. Orion) (SALE MANAGER) - Phone: (+84) 905.648.436 - Email: tas.info@tasvina.com